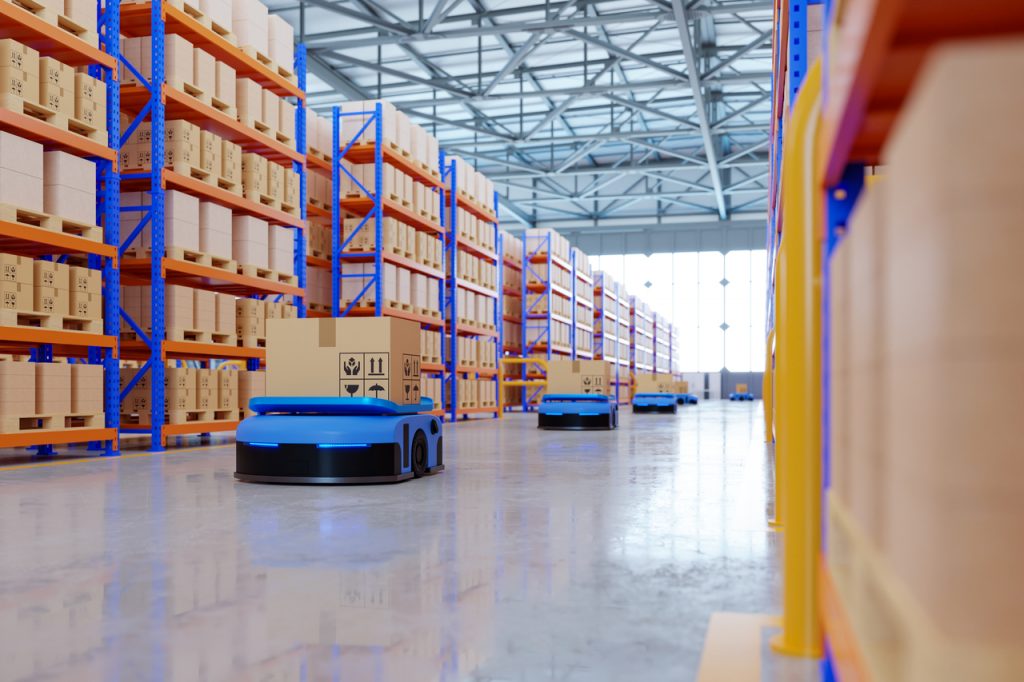
5 Essential Warehouse KPIs You Need To Track
March 31, 2021
What are the essential warehouse KPIs you need to track?
- Inventory turnover
- Inventory accuracy
- Receiving efficiency
- Put away efficiency
- Order picking accuracy
Key performance indicators (KPIs) provide a standard to measure business performance against defined goals. Without KPIs defining progress, your company cannot gauge areas that need improvement and compare performance to that of your competitors. Any warehousing in the Philippines that prioritizes KPIs will garner logistics efficiency. Then, your business can dive deeper into the areas of improvement in the supply chain and assess subordinate KPIs. This article delves deeper into the 5 warehouse KPIs you need to track. Continue reading to learn more.
Inventory Turnover
Inventory plays a vital role in warehousing—having too much can result in costly challenges, as can having too little. The higher the inventory turnover rate, the better. The possible issues that are interrelated with low inventory turnover are too many stocks and too few sales.
Inventory turnover is an essential warehouse KPIs to track because it measures the frequency at which you sell out your stocks during a period of time. By using this KPI, you can manage your inventory better by gauging consumers’ buying behaviors. Thus, you can adjust purchasing and production habits accordingly to aim for a higher inventory turnover rate. In the end, this results in enhanced cash flow management and profitability.
It is essential to know if you are stocking up on the products that are not selling. Doing so helps avoid carrying the burden of additional inventory expenses and not generating sales effectively. To add to that, too much inventory takes up significant shelf space and decreases your warehouse’s overall efficiency.
Inventory Accuracy
Inventory accuracy is a warehouse KPI that businesses should also pay close attention to. If the accuracy of physical inventory is compromised, you can experience unnecessarily high expenses, unexpected order returns, and a significant drop in customer satisfaction rate.
Think about it. If you end up with inventory inaccuracies, you can deliver the wrong items to customers. In an era where customer satisfaction heavily dictates organizational success and where negative word-of-mouth of services can have negative impacts, you’d want to track inventory accuracy.
Keep in mind that visibility is key to an efficient warehouse. Thus, the best way to measure inventory accuracy is to compare how many and which items are in stock to what is actually recorded in the database. Conduct regular checks against your database and validate records.
Receiving Efficiency
Receiving is the term that involves the time when the new inventory enters a warehouse. The biggest factor to understand about receiving is that if it is done inaccurately or slowly, it will have a ripple of negative effects and make overall warehouse operations ineffective.
From the labor hours involved in receiving goods, checking received orders against purchase orders, to the rate at which multiple inventories that arrive each week is processed — receiving efficiency proves to be a KPI that requires tracking. Your warehouse will also likely receive return-to-vendor inventory and returned inventory (both good and damaged) from customers.
Receiving efficiency can be increased in several ways which include partnering with a warehousing company that hires highly-trained staff, creating scannable bar-code stock-keeping units (SKUs), and organizing the SKUs to a specific warehouse location. All these efforts will speed up the receiving process.
Put-Away Efficiency
Once you have received inventory, you must put them away. This means placing each item at a designated location for the most convenient retrieval. As a result, this reduces order lead time and streamline warehouse processes.
Put-away efficiency KPIs involve measuring the cost to put away items per line, the percentage at which items are put away accurately, and total cycle time to complete the tasks.
Tracking put-away efficiency will give you a clear picture of potential bottlenecks in the warehousing process such as inaccuracies and scarcity of labor. If your put-away efficiency is not consistent, check if inventory is consistently being mixed up by employees.
Order Picking Accuracy
Given that the main role of warehouses is to satisfy customer needs, measuring for ordering picking accuracy is one of the most important KPIs needed to be tracked. An incorrectly picked order means incurring costs from returned items. According to a survey, 54% of customers say they’ve returned online orders because they received the wrong item.
There are many different ways to improve your order picking accuracy to get the right items for your customers. This can include tracking order accuracy rates, bar-code labeling products properly, and have a reliable inventory management system.
Key Takeaway
This article delves deeper into the warehouse KPIs you need to track. Defining and improving each of these warehouse KPIs will drive customer satisfaction and hence, cost-effectivity in every aspect.
Experienced companies that offer warehousing in the Philippines can help improve your KPI performance. Learn about what Airspeed can offer to grow and protect your business today. Click here to know how we can introduce these core KPIs into your warehouse.